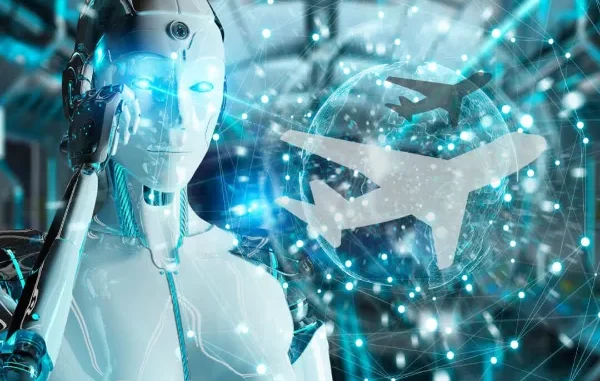
Turbine oil functions as an essential element for maintaining the smooth operation of machines. The lubricating substance minimizes friction while defending components against wear and damage. The effectiveness of turbine oil decreases when maintenance is inadequate, which results in both expensive repairs and operational stoppages. A few basic maintenance procedures will both lengthen the lifespan of turbine oil and maximize turbine operational efficiency.
1. Regular Oil Analysis
Regular oil analysis enables early detection of potential issues. Performance suffers when contaminants mix with the oil while oxidation and viscosity changes occur. Testing oil samples reveals important information about its current state. Early detection of problems through timely corrective action helps avoid more significant equipment failures. Lab reports detect deviations, which lead technicians to make necessary adjustments. Scheduled oil quality checks enable reliable equipment operation while preventing unexpected breakdowns and extending equipment lifespan.
The practice of regular monitoring helps reduce equipment downtime and maintenance expenses. The early identification of potential problems enables both operational stability and effective resource distribution. The proactive analysis of oil helps organizations prevent expensive maintenance costs, which results in longer equipment life and better operational efficiency throughout the entire lifespan.
2. Proper Contamination Control
Dirt, water, and debris degrade turbine oil. Even small particles can cause damage over time. Using high-quality filters removes impurities before they circulate through the system. Seals and breathers prevent external contaminants from entering. Water contamination leads to rust and oxidation, reducing oil effectiveness. Proper storage also plays a role. Keeping oil containers sealed and stored in clean environments minimizes exposure to harmful elements.
Regular maintenance of filters, seals, and breathers ensures optimal protection. Implementing proper handling procedures reduces risks, prolongs oil life, and maintains turbine efficiency, ultimately reducing the likelihood of costly repairs and unexpected downtime.
3. Effective Temperature Management
Temperature affects oil performance. Excessive heat speeds up oxidation, reducing its lifespan. Low temperatures cause thickening, making circulation difficult. Monitoring operating temperatures ensures oil remains within the ideal range. Heat exchangers and coolers help regulate conditions, preventing overheating. Regularly checking for hot spots or blockages in cooling systems maintains steady performance. Addressing temperature fluctuations prevents premature oil degradation. Implementing temperature control measures, such as proper insulation, ensures consistent viscosity and performance. Timely identification of temperature irregularities allows for quick corrective actions, minimizing potential damage and extending the operational lifespan of the equipment while maintaining optimal efficiency.
4. Timely Oil Replacement
Even with good maintenance, oil eventually breaks down. Over time, it loses its ability to lubricate effectively. Following manufacturer recommendations for oil change intervals helps avoid performance issues. Factors like operating hours, environmental conditions, and load variations determine replacement schedules. Using high-quality oil, such as Eastman turbine oil, ensures long-lasting efficiency.
Draining old oil completely before refilling prevents mixing and preserves the new oil’s integrity. Monitoring oil conditions between changes allows for early detection of potential issues. Regular oil changes, coupled with proper filtration, optimize equipment performance, extend service life, and reduce the risk of unexpected failures or downtime.
5. System Inspections and Upkeep
Keeping turbine systems in good condition extends oil life. Worn-out seals, loose fittings, or leaks contribute to contamination and inefficiency. Inspecting for leaks and repairing damaged components prevents oil wastage. Cleaning reservoirs, pipes, and filters reduces sludge buildup. A well-maintained system requires less oil replacement and operates more efficiently. Scheduling routine inspections keeps everything running optimally.
Regular checks for wear and tear on critical components help detect problems before they escalate. Ensuring tight seals and proper alignment reduces the risk of contamination and enhances overall system performance. Proactive maintenance improves reliability, reduces downtime, and lowers long-term operational costs.
Conclusion
Maintaining turbine oil efficiency does not require complicated steps. Simple habits like regular testing, contamination control, and temperature management make a big difference. Changing the oil on time and keeping systems in good shape also helps. These efforts improve performance, reduce costs, and extend the life of turbines. Small actions lead to long-term benefits, keeping operations smooth and trouble-free.
Regular monitoring of oil condition, along with timely repairs and maintenance, ensures consistent functionality. By addressing issues early, costly downtime and equipment failures are minimized, ultimately leading to higher productivity and more efficient resource use. Prevention is key to maximizing system lifespan.
Leave a Reply