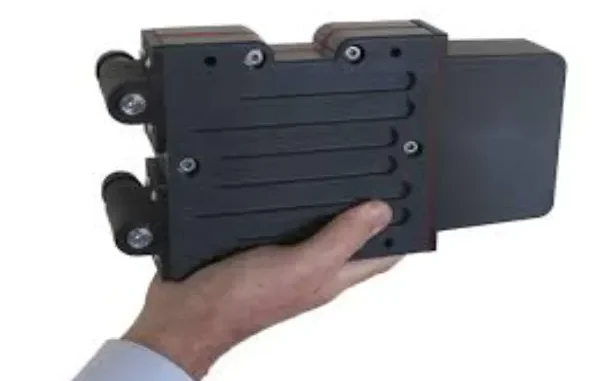
Resistors play a key role in thermal management and efficiency in electric vehicles, which is why choosing the right power resistor goes a long way in enhancing system design. The world is continuously leaning towards energy-efficient systems like electric and hybrid vehicles, wind turbines, and composite aircraft. This has also led to a corresponding increase in the demand for electronic resistors.
Today, electrical controls are swiftly replacing large and heavy mechanical devices with reduced lifespans resulting from frictional wear and tear. However, system designs are not fully optimized by conventional electronic components. For electrical devices to operate at safer temperatures, there’s a need for a reduction in their size and weight.
The maximum operating temperature of resistors at a constant power level increases with a corresponding decrease in mass and size, making it challenging to completely reduce temperature, size, and weight. This challenge has led to the innovation of new design concepts with efficiency and heat dissipation in mind. Basically, balancing efficiency and heat dissipation is vital for meeting optimal operating conditions and this article will help you understand how this is achieved with power resistors for electric vehicles.
Effect of Reducing System Size on Power Resistors
Reducing the size of systems that were originally designed to handle continuous power and large surges requires considering the available space and mass of the system. This should also include defining the internal package temperature and operating environment for appropriate material selection and internal device consideration.
An effective way of reducing the mass and size of resistors is to eliminate the thermal mass. However, this further increases the operating temperature of the resistor and surrounding electronic components. Power resistors are designed to bridge this gap. Reducing the mass and size of power resistors can be achieved by using the construction and material used on the entire module. For instance, if the electric vehicle operates on a 33- to 650 V dc high-voltage bus, insulated gate bipolar transistors are used instead of conventional relay power switching. Power resistors help reduce the current in the charging systems. Also, they are easy to mount on heatsinking devices.
Alternate Methods for Heat Dissipation
There are designs where the considerations above may not apply, but they still require heat and power dissipation. In such instances, there’s a need for alternate approaches for efficient power dissipation. This can be the use of an existing thermal mass in the system to ensure that there’s no further increase in the weight of the entire construction.
Thermal Management of Power Resistors on a Relative Scale
The focus of power resistors has mostly been on power and heat dissipation in kilowatts. However, because most resistors generate heat, the limitation has mostly been on placement options. The printed circuit board on the control circuit level also has thermal limitations, and this is usually with respect to the type of material that is used as substrate.
Even though surface mount devices are usually below the 1-W rating, the big question is what will happen when more than that limit is required. This is also a concern when the temperature of the operating environment is 85, 125, or 200 degrees for some aerospace, downhole drilling, and automotive applications.
Powering the Future: The Role of Resistors in Electric Vehicles
It’s no doubt that electric vehicles are the future of the automotive industry. Today it has become a standard within the industry and no longer a luxury as it was many years ago. Most automotive makers are now joining Tesla in developing cost-effective and affordable electric vehicles. With this continued growth and increase in the availability of electric vehicles, there’s a need for more robust charging stations.
Countries are also investing in electric vehicle charging stations today, and an example is the United States, which invested $5 billion in these stations in 2022. However, in addition to the availability of charging stations, there’s also a need for a reduction in charging time. Today, there are currently three types of charging speeds and types, which are:
- Level 1 chargers are mostly available in residential areas and offer a 12v AC outlet. These chargers can charge battery electric vehicles to 80% within 40-50 hours, while plug-in hybrid electric vehicles take up to 6 hours.
- Level 2 offers up to 240 volts for residential use and 208 volts for commercial use. They are the options commonly found in public charging stations.
- Direct current fast charging is commonly found in places with heavy traffic, and they are designed to provide rapid charging. Battery electric vehicles can be fully charged within 20 minutes with these chargers.
Regardless of the charging speed, there’s a need to regulate the heat that is generated when charging. Without this, the battery will overheat and potentially cause other hazards, and this is where resistors are handy. The currently available resistors are cost effective and reliable when it comes to current control which also helps in heat control when charging.
One of the leading manufacturers of these resistors is TT Electronics, with a wide range of sense resistors on the market for battery management systems. It’s vital to choose the right resistor technology, especially in terms of its value and rating. However, most people don’t usually understand the importance of secondary factors like consistency, surge performance, safety and reliability when there’s current overload.
Conclusion
Resistive components are vital in electronic systems and surge energy. Even though the creation of heat from devices cannot be totally avoided, there are approaches that can help in reducing heat dissipation. These approaches also don’t add to the size and mass of the system design. In some cases, the heat can be directed to components that can generate and handle heat.
Another approach that is used is the use of a thick film to effectively handle heat dissipation issues from resistors. This approach also allows for weight and space savings and further increases the efficiency of the system.
Leave a Reply