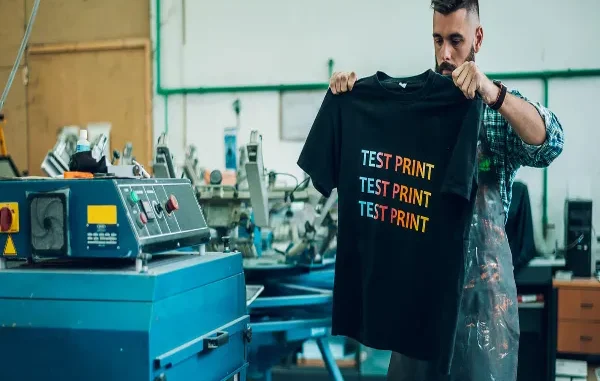
T-shirt printing has come a long way over the years, evolving from simple designs to high-quality prints that can showcase intricate artwork, logos, and creative concepts. Whether you’re looking to create custom t-shirts for your business, a special event, or just for personal use, understanding the entire t-shirt printing process can help you achieve the best results. In this post, we’ll guide you through the steps of producing high-quality printed t-shirts, from design creation to final delivery.
Understanding the T-Shirt Printing Process
T-shirt printing is the art of applying a design to a fabric, typically a t-shirt, using various techniques and technologies. The process begins with your concept and ends with a tangible product. The choice of printing technique depends on several factors, including design complexity, fabric type, and order quantity. Understanding each step of the t-shirt printing process helps ensure that the final product meets your expectations and delivers quality every time.
Step 1: Design Creation
The first step in the t-shirt printing process is the creation of the design. This is where the magic happens—your ideas are brought to life, ready to be printed. You’ll want to use design software that allows you to create high-quality graphics. Popular tools like Adobe Illustrator, CorelDRAW, and even free options like Canva can help you create a professional-looking design. It’s important to ensure that your design is suitable for printing by paying attention to specific factors such as resolution and format.
When it comes to design resolution, aim for 300 DPI (dots per inch) to ensure a crisp, clear print. A lower resolution could lead to pixelation and blurry prints, which will reduce the quality of your final product. For the best print results, you should save your designs in vector formats, such as .AI or .SVG, as these can be scaled without losing quality. If you’re working with raster images (like photos), make sure they’re large enough and high-quality.
The design’s color palette is also crucial. Simple, bold designs tend to work best for printing, while overly complex or gradient-heavy images might not translate well onto fabric. If your design uses specific colors, ensure they are aligned with the color options available for printing. In some methods, like screen printing, precise color matching is critical for consistency across large batches.
Step 2: Choosing the Right Fabric
The fabric you choose for your t-shirts plays a significant role in the final print quality. Cotton is the most common choice because it is soft, breathable, and easy to print on. However, other materials like polyester or fabric blends are also popular depending on the desired look and feel. Polyester, for instance, is ideal for sublimation printing, which works by embedding the ink directly into the fabric.
When selecting fabric, it’s essential to consider its weight and texture. A heavier fabric may provide a better surface for printing, resulting in a more durable design. However, the material’s texture—whether it’s smooth or rough—can affect how well the ink adheres to the surface. Fabrics that are too coarse or have too much stretch may not deliver as clean of a print.
Before printing, fabrics often undergo a pre-treatment process to ensure that the ink adheres properly. This is especially important for methods like Direct-to-Garment (DTG) printing, where the ink is applied directly to the fabric. Pre-treatment can involve applying a special coating to the fabric to allow the ink to bond, ensuring vibrant, long-lasting prints.
Step 3: Selecting the Printing Technique
The next critical step is choosing the right printing method. There are several options available, each suited for different types of designs and orders. Here’s a brief overview of the most popular techniques:
Screen Printing: This is one of the most widely used methods, especially for larger orders. It involves creating a stencil (or “screen”) for each color in the design. The ink is then pushed through the screen and onto the fabric. Screen printing is ideal for simple designs with few colors and is known for producing long-lasting, vibrant prints.
Direct-to-Garment (DTG) Printing: DTG printing uses specialized inkjet technology to apply the design directly to the fabric. It’s an excellent option for complex, multicolored designs or small print runs. This technique works best with cotton fabrics and produces highly detailed images. DTG is perfect for custom t-shirts with intricate designs or photo prints.
Heat Transfer and Vinyl Printing: Heat transfer printing involves using a heat press to transfer the design from a special paper to the fabric. Vinyl printing uses a similar method, but instead of ink, vinyl sheets are cut into the design and then heat-pressed onto the fabric. Both techniques are great for small batches and custom designs, but they may not offer the same durability as screen printing or DTG in the long run.
One newer method gaining attention is DTF printing (Direct-to-Film), which is a versatile technique that combines elements of both screen printing and DTG. DTF printing involves printing designs onto a film that is then transferred onto the t-shirt. This method works well for complex designs and offers excellent color accuracy, and it can be used on a wide range of fabrics, making it an exciting alternative for custom t-shirt printing.
Step 4: Printing the Design
Once the fabric and printing method have been chosen, it’s time to transfer the design onto the t-shirt. During this phase, the focus should be on achieving the best possible result by using the correct settings and equipment for the chosen printing technique. Whether you’re working with a screen printer, a DTG machine, or a heat press, ensuring that your equipment is calibrated and in top working order is essential.
For methods like screen printing, quality control during the printing process is crucial. Each screen should be checked for consistency to prevent misprints. Similarly, with DTG printing, it’s important to ensure that the ink is applied evenly to maintain color vibrancy and design accuracy.
One key tip for achieving high-quality prints is to avoid overloading the print with too many intricate details that may be difficult to reproduce. Keep in mind that some printing methods, like screen printing, work best for simpler designs with fewer colors.
Step 5: Post-Processing and Curing
After the design has been printed, the next step is curing the ink. This process ensures that the ink bonds properly to the fabric and that the design is durable and vibrant. Curing typically involves using a heat press or conveyor dryer to apply heat to the printed t-shirt, which helps the ink set into the fabric.
Curing is especially important for techniques like DTG printing, where the ink sits on top of the fabric, rather than being absorbed into it. If the curing process isn’t done correctly, the ink may fade or crack over time. Quality control checks during this stage are vital to ensure that each shirt meets the desired standards.
Step 6: Packaging and Delivery
Once the t-shirts have been printed and cured, they’re ready to be packaged and shipped. Proper packaging is essential for protecting the prints during transit. T-shirts should be folded neatly and placed in protective poly bags to prevent any damage or dirt from affecting the design. Additionally, clear labeling and order tracking are critical for ensuring timely delivery.
For businesses, having a reliable shipping method ensures customer satisfaction. A smooth delivery process, including accurate tracking and secure packaging, will help build a positive reputation and encourage repeat customers.
Conclusion
From design creation to delivery, the process of high-quality t-shirt printing involves several steps that require attention to detail and a commitment to quality. By understanding the various techniques available and how each step contributes to the final product, you can ensure that your custom t-shirts not only look great but are also durable and long-lasting. Whether you’re designing shirts for personal use or launching a custom apparel business, knowing the ins and outs of the printing process will help you achieve outstanding results.
Leave a Reply