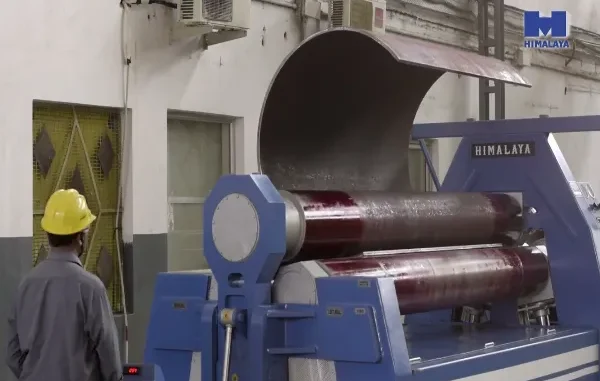
In the world of metal fabrication, precision and efficiency are paramount. At Brandywine Valley Fabricators in Pennsylvania, we continually strive to deliver high-quality, custom metal solutions that meet our clients’ unique needs. Two fundamental processes that play a crucial role in our production capabilities are sheet rolling and plate rolling. Although these terms might sound similar, they refer to distinct processes with specific applications. In this post, we’ll dive into the details of sheet rolling, compare it with plate rolling, and explain how understanding these differences can help you choose the right fabrication process for your project.
What is Sheet Rolling?
Sheet rolling is a metal forming process where a flat sheet of metal is passed through a series of rollers to produce a curved or cylindrical shape. This process is widely used in industries that require precision-formed components such as ducts, pipes, and various decorative elements. The primary advantages of sheet rolling include:
- Precision and Consistency: Advanced rolling machines, including CNC-controlled systems, ensure that each sheet is rolled to exact specifications, reducing material waste and the need for additional finishing.
- Versatility: Sheet rolling can be used to form a variety of shapes and sizes, making it an ideal process for both custom fabrication and large-scale production.
- Efficiency: With modern equipment, sheet rolling is both fast and cost-effective, allowing manufacturers to meet high-volume demands without compromising on quality.
What is Plate Rolling?
Plate rolling, on the other hand, involves bending thicker metal plates rather than thin sheets. This process is critical when working with heavy-duty materials that require additional strength and durability. Plate rolling is often used in the fabrication of structural components, heavy machinery parts, and large architectural elements. Key benefits of plate rolling include:
- Strength and Robustness: Plate rolling produces components that can handle higher loads and stresses, making them ideal for structural applications.
- Customization: Like sheet rolling, plate rolling can be tailored to specific dimensions and curvatures, ensuring that the final product meets precise engineering standards.
- Application in Heavy Industries: Industries such as construction, automotive, and energy frequently use plate rolling to fabricate parts that demand superior strength.
Key Differences Between Sheet Rolling and Plate Rolling
While both sheet and plate rolling involve the bending of metal, several factors distinguish one from the other:
Material Thickness
- Sheet Rolling: This process is used for thinner, more flexible materials. The typical sheet metal used in sheet rolling is lighter and easier to form into precise curves.
- Plate Rolling: Plate rolling deals with thicker, heavier metals that require more force to bend. The higher thickness translates into components with greater structural integrity.
Applications
- Sheet Rolling: Common applications include the manufacture of HVAC ducts, automotive body parts, and decorative architectural features. The focus here is often on creating aesthetically pleasing and accurately dimensioned products.
- Plate Rolling: This process is crucial in producing load-bearing structures, such as support beams, roll-formed panels for construction, and industrial machinery parts, where strength is of utmost importance.
Equipment and Process Complexity
- Sheet Rolling: Modern sheet rolling machines are highly automated and capable of producing intricate curves with minimal human intervention. They are designed for high-volume production and offer quick turnaround times.
- Plate Rolling: Due to the heavier materials involved, plate rolling machines are built to withstand higher pressures. The process may require additional steps to ensure that the rolled plate maintains its strength and does not crack or deform improperly.
Why Understanding the Differences Matters
At Brandywine Valley Fabricators, we recognize that choosing between sheet rolling and plate rolling can significantly impact the performance and cost-effectiveness of your project. Understanding the differences allows you to:
- Select the Right Process: Depending on your project’s requirements—whether you need lightweight, decorative components or heavy-duty structural parts—you can choose the appropriate rolling process.
- Optimize Material Usage: By knowing the material thickness and required strength, you can avoid unnecessary waste and reduce overall production costs.
- Enhance Product Quality: Precision in metal forming leads to higher-quality products. Our expertise in both sheet and plate rolling ensures that every component we fabricate meets stringent industry standards.
Applications at Brandywine Valley Fabricators
Our facility is equipped with advanced rolling machinery capable of handling both sheet and plate rolling processes. Here are a few examples of how we apply these techniques:
- Architectural Elements: Using sheet rolling, we create custom curved facades, window frames, and decorative metalwork that add a modern touch to buildings.
- Structural Components: Plate rolling is essential in producing robust support beams, roll-formed panels, and machinery parts that demand high strength and durability.
- Automotive and Industrial Parts: We offer tailored solutions for industries that require both precise aesthetics and structural integrity, ensuring that our rolled metal components meet the diverse needs of our clients.
Conclusion
Metal fabrication is a complex field that requires a deep understanding of various processes to produce high-quality products. Sheet rolling and plate rolling are two critical techniques that, while similar in concept, serve very different purposes. At Brandywine Valley Fabricators, our commitment to innovation and precision means we use the best process for each specific application, ensuring that our clients receive the highest standard of workmanship.
If you’re planning a project and need expert advice on whether to opt for sheet rolling or plate rolling, we invite you to contact our team. Our experienced engineers and technicians are here to help you navigate your options and choose the process that best aligns with your goals. Visit our website or call our Pennsylvania office to learn more about our custom metal fabrication solutions and how we can help bring your vision to life with precision and efficiency.
Leave a Reply